Fertigungs- und Montage von Windkraftanlagen
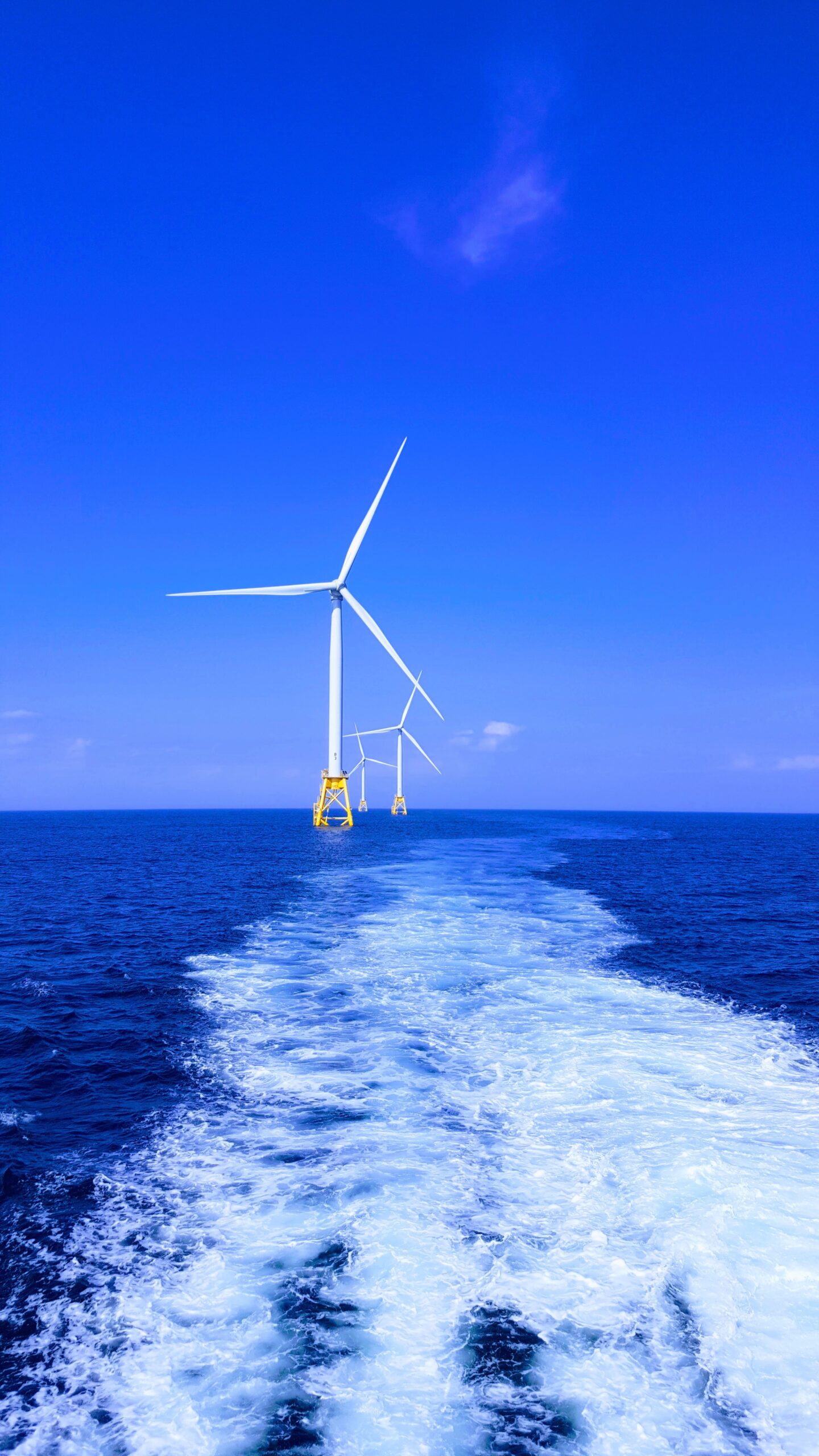
Haben Sie sich schon einmal gefragt, wann und wie sich die erneuerbare Energie von einfachen Windmühlen auf Bauernhöfen über Windkraftanlagen, die das Landschaftsbild auf dem Land dominieren, zu schwimmenden Offshore-Windkraftanlagen entwickelt hat?
Die Geschichte der Nutzung von Wind als erneuerbare Energiequelle ist faszinierend. Die erste funktionierende Windmühle in Großbritannien stammt aus dem Jahr 1665, als die Arbeiten an der Outwood Mill in Surrey begannen. Es ist die dienstälteste Windmühle in Großbritannien, die Windenergie nutzt, um mit mechanischer Kraft Getreide zu Mehl zu mahlen.
In dieser Zeit gab es vier Arten von Windmühlen: Sunk-Post-Mühlen, offene Bockwindmühlen, Smock-Mühlen und Turmwindmühlen. Die meisten wurden entweder zum Mahlen von Getreide oder als Wasserpumpe verwendet, um das Vieh mechanisch mit Wasser zu versorgen.
Erst 1877 wurde in Schottland von einem Elektroingenieur, Prof. James Blyth vom ehemaligen Anderson’s College of Glasgow, der heutigen Strathclyde University, die erste Windturbine der Welt zur Stromerzeugung gebaut. Prof. Blyths Windkraftturm war etwas mehr als 10 Meter hoch. Das Windrad diente als mechanische Energiequelle, die mit Hilfe eines Dynamos sein Ferienhaus in Marykirk beleuchtete. Überschüssiger Strom wurde in Akkumulatoren geleitet, obwohl der überschüssige Strom der Stadt für die Straßenbeleuchtung angeboten wurde. Die Einheimischen lehnten das aus Aberglauben ab, denn damals hielten die Menschen Elektrizität für das „Werk des Teufels“.
Die moderne Ära des Baus von Windkraftanlagen
Im Laufe der Jahre, in denen das Wissen wuchs und die Nachfrage nach alternativen Energiequellen stieg, zeigten Analysen und Tests, dass Windkraftanlagen und -turbinen zuverlässige Stromquellen sind, indem sie kinetische Energie aus Wind in rotierende mechanische Energie umwandeln. Ein Generator wandelt dann die Rotationsenergie in Elektrizität um. Analysen zeigen, dass der Prozess einen optimalen Wirkungsgrad von 59,26 % (bekannt als Betz-Grenze) aufweist, wobei aktuelle Windkrafttürme und -turbinen bei der Umwandlung von Windenergie in nutzbare Energie einen Wirkungsgrad von 35 % bis 45 % erreichen können.
Die heutigen Windkraftanlagen sind weitaus größer als noch vor Jahrzehnten und können Megawatt pro Turbine erzeugen, wodurch ganze Städte mit Strom versorgt werden können, anstatt nur ein paar Straßenlaternen.
Die durchschnittliche Größe europäischer Windturbinen von 3 MW hat Rotorblätter mit einer Länge von 50 bis 100 Fuß, die bis zu 1.500 Haushalte pro Turbine mit Strom versorgen können. Größere Windturbinen mit 7,5 MW (die bisher größten) haben Rotorblätter mit einer Länge von 60 Metern. Die höchste britische Onshore-Windturbine ist 125 Meter hoch. Die 8,4-MW-Offshoreturbine vor der Küste von Aberdeen stellt mit einer Höhe von 191 Metern alles in den Schatten.
Die gestiegene Nachfrage nach erneuerbaren Energien ist eine treibende Kraft hinter der großflächigen Produktion von Windparks in ganz Europa und auf der ganzen Welt. Von allen Arten grüner Energie ist die Windkraft bei weitem die effizienteste in Bezug auf Herstellungs- und Betriebskosten.
Allein in Europa sind 4.149 Windturbinen aus 94 Windparks in 11 Ländern an das Stromnetz angeschlossen und erzeugen 15.780 MW. Diese Zahlen werden voraussichtlich noch steigen, da das Pariser Abkommen das ehrgeizige Ziel vorgibt, bis 2030 32 % der Energie aus erneuerbaren Quellen zu erzeugen.
Windturbinen werden immer größer, da der Wind in größerer Höhe schneller weht und die Turbinen so mehr kinetische Energie einfangen können.
Um den Großteil der nutzbaren Energie einzufangen, sind sich die Windparkbetreiber der Bedeutung der Fertigungsanforderungen bewusst.
Die Fertigungsanforderungen für die Herstellung von Windtürmen und -turbinen
Die Hersteller sind sich der Notwendigkeit bewusst, auf industriellem Maßstab erneuerbare Energie aus Windkraftanlagen zu erzeugen. Nicht die Art, die ein Haus mit Strom versorgt, sondern die Art von Windkraftanlagen, die ein Haus mit einer einzigen Umdrehung mit Strom versorgen können.
Dies erfordert einen robusten Herstellungsprozess, der in großem Maßstab durchgeführt werden kann. Ob für Onshore-Windparks oder eine Offshore-Turbine wie die riesige 8,4-MW-Turbine … es werden schwere Maschinen benötigt.
Bei der Herstellung solcher gigantischen technischen Meisterwerke werden schwere Stähle in kleineren Größen von Stahlrohren (sogenannten „Cans“) verwendet, die in der Regel 2,74 m lang sind und einen Durchmesser von 2,44 bis 4,57 m haben. Diese werden in Fabriken entlang einer Fertigungsstraße bzw. einer Growing Line verarbeitet, die konventionelles und fortgeschrittenes Schweißen in verschiedenen Phasen erfordert.
Über Fertigungsstraßen für Windkraftanlagen
In Fertigungsstraßen für Windkraftanlagen werden zahlreiche Fertigungsmaschinen zur Automatisierung eingesetzt, um Kosten zu senken und die Schweiß- und Fertigungsqualität zu verbessern. Die in einer Fertigungsstraße für den Windenergiesektor eingesetzten Maschinen sind unterschiedlichster Art. Mit einer Tankdrehrolle lassen sich Metallbleche unterschiedlicher Stärke zu Stahltanks formen. Ein Schweißrotator kann dann zum mechanischen Drehen des Tanks verwendet werden, während eine andere Maschine eine äußere Umfangsschweißnaht anbringt, um den Tank abzudichten. Die Bediener steuern die Rotationsgeschwindigkeit und überwachen die Schweißqualität. Die Automatisierung der Schweißprozesse für Umfangs- und Längsnähte ermöglicht es den Herstellern von Windkraftanlagen, die Produktion und Qualität zu steigern und gleichzeitig die Gemeinkosten zu senken. Sobald die Kessel versiegelt sind, können Positionierer und Drehtische als Teil der Produktionslinie für verschiedene Schweißprozesse verwendet werden, bevor sie maschinell zu einem Fit-up-Bed transportiert werden, wo jeder Behälter dann zusammengebaut werden kann, um zum Zielort transportiert zu werden.
Das folgende Video zeigt den Aufbau und die Vorführung einer Fertigungsstraße für Windkraftanlagen.
Die Rolle von Schweißautomaten
Schweißrotatoren werden zum Drehen großer Behälter verwendet, sodass Schweißer in allen Bereichen in jedem Winkel jedes Rohrabschnitts arbeiten können. Sie können sowohl entlang der Längsnähte als auch am Umfang schweißen. Automatisierte Unterpulver-Schweißsysteme ermöglichen Stumpfschweißungen über mehrere Durchgänge mit minimaler Arbeitsbelastung für den Bediener. Das Schweißen der Außenseite der Behälter erfolgt mit einem Schweißkopf, der an einer Säule und einem Ausleger aufgehängt ist, wodurch der Prozess aller äußeren Schweißvorgänge automatisiert wird.
Da die Höhe von Windkraftanlagen zunimmt, werden in allen Teilen des Produktionsprozesses dickere Stähle verwendet. Je dicker der Stahl ist, desto intensiver ist der Schweißprozess für den Bediener, was häufig zu Erschöpfung führt.
Die Konstruktion von Windkraftanlagen ist fortschrittlich und wettbewerbsfähig. Prozesse müssen sowohl vor Ort als auch außerhalb automatisiert werden.
Redrock Automation bietet die Maschinen, die Windturbinenhersteller benötigen, um ihre Betriebsabläufe zu optimieren, die Kompetenz und Effizienz aller Schweißphasen zu steigern und gleichzeitig die Ermüdung der Bediener zu reduzieren. Darüber hinaus können die Bediener den Prozess im Auge behalten und so durchgehend Schweißnähte von höchster Qualität sicherstellen.
Unsere Rolle in der Fertigung von Windkraftanlagen
Als Experten für Schweißautomatisierung bietet Redrock eine Reihe von Dienstleistungen für Hersteller von Türmen für Windkraftanlagen an, beginnend mit einer Fachberatung nach einer ersten Anfrage.
Von Anfang an besprechen wir die Projektziele und finden dann heraus, wo wir uns einbringen können.
Einige Bereiche, in denen wir tätig sind:
- Vor-Ort-Beratungen
- Lieferung und Installation von Geräten zur Verbesserung der Gesundheits- und Sicherheitsstandards
- Lieferung einer Reihe von Spezialschweißgeräten zur Steigerung des Durchsatzes
- Schulung der Bediener im fachgerechten Umgang mit Maschinen
- Wartung und Instandhaltung von Schweißgeräten, sei es im Rahmen eines Mietvertrags oder einer erweiterten Garantie, die in unserem gesamten Produktkatalog verfügbar ist.
Unser Ziel ist immer dasselbe – Lösungen bereitzustellen, um Geschäftsziele zu erreichen. Manchmal führen wir schlüsselfertige Lösungen aus unserer Werkstatt ein, die sofort installiert und von Bedienern geschult werden können. In anderen Fällen sind Projekte so einzigartig, dass unser Ingenieurteam maßgeschneiderte Maschinen entwirft, die von uns hergestellt werden, um den Anforderungen spezifischer Projekte gerecht zu werden, die speziell angefertigte Maschinen erfordern.
Unsere Rolle ist es, Partner zu sein
… Partner, die Schweißautomatisierungsgeräte bereitstellen, die die Geschäftsziele erfüllen und übertreffen, indem sie die Produktivität und die Arbeitsbedingungen verbessern und oft eine schnelle Rendite erzielen.
Wir sind weltweit führend in der Herstellung, Lieferung und Installation von Schweißautomatisierungsgeräten, die den heutigen Anforderungen an die Herstellung robuster Windtürme aus hochbelastbarem Stahl gerecht werden.
Wir bieten Herstellern von Windkraftanlagen einen umfassenden Service, der von der Beratung über die Lieferung und Installation bis hin zur Schulung der Bediener reicht und unsere Geräte im Rahmen einer Miete oder unserer erweiterten Garantie wartet.
Mit strategisch günstig gelegenen Niederlassungen auf der ganzen Welt ist Redrock der EINZIGE ANSPRECHPARTNER für Hersteller von Türmen für Windkraftanlagen. Eine Anlaufstelle für automatisierte Schweißlösungen.